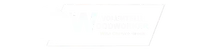
What If
11/1/2024 | 26m 46sVideo has Closed Captions
Host Charles Brock is joined by visionary woodwork John Lucas.
Described as a genius by many, “What if” fuels John Lucas’s vision and works of art. John describes the processes he uses to create his unconventional works.
Volunteer Woodworker is presented by your local public television station.
Distributed nationally by American Public Television
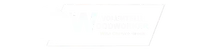
What If
11/1/2024 | 26m 46sVideo has Closed Captions
Described as a genius by many, “What if” fuels John Lucas’s vision and works of art. John describes the processes he uses to create his unconventional works.
How to Watch Volunteer Woodworker
Volunteer Woodworker is available to stream on pbs.org and the free PBS App, available on iPhone, Apple TV, Android TV, Android smartphones, Amazon Fire TV, Amazon Fire Tablet, Roku, Samsung Smart TV, and Vizio.
Providing Support for PBS.org
Learn Moreabout PBS online sponsorship(cheerful music) - Welcome to "The Volunteer Woodworker," I'm your host Charles Brock.
Come with me as we drive the back roads, bringing you the story of America's finest woodworkers.
(cheerful music) (cheerful music continues) We're going to Cookeville, Tennessee to meet John Lucas.
He never lets his skills dictate his works of art.
The term, what if, always fuels the vision and the process.
Described as a genius by many, let's meet John and see his work.
(cheerful music) - [Announcer] "Volunteer Woodworker" is funded in part by, since 1970 Whiteside Machine Company has been producing industrial grade router bits in Claremont, North Carolina.
Whiteside makes carbide bits for edge forming, grooving, and CNC applications.
Learn more at whitesiderouterbits.com.
Real Milk Paint Company makes VOC-free non-toxic milk paint available in 56 colors.
Milk paint creates a matte wood finish that can be distressed for an antique look.
Good Wood Nashville designs custom furniture and is a supplier of vintage hardwoods.
Keri Price with Keller Williams Realty has been assisting middle Tennessee home buyers and sellers since 2013.
Mayfield Hardwood Lumber, supplying Appalachian hardwoods worldwide.
Anna's Creative Lens, crafters of resin on wood decorative arts.
- John Lucas.
Wow, love being in your shop.
Tell us how you got started with this.
- Well, I started woodworking right after college, actually in college a little bit.
I bought a router and scrolls and jigsaw and stuff, started playing.
And when I got the job at Tennessee Tech as a photographer, one of the things I was doing was photographing for the Appalachian Center for Crafts, photographing all their craft work.
And I met a man named Joe Looper.
And I'd been turning wood, I bought a shopsmith and I was playing and I was doing a little bit of turning, a little whatever.
Joe Looper was really, really good at turning green wood.
And so Joe kind of took me under his wing and got me going in that direction.
- You had cheaper wood to turn because it's plentiful.
- When I moved here to Tech, I'd lost two or three jobs due to layoffs, and I didn't have much money, I was working 40, 50, 60 hours a week.
Didn't have a lot of time to build furniture anymore.
And then when Joe got me into green wood working, I lived out in Gainesboro, had the woods all around me.
It was the perfect hobby.
I could go downstairs and, you know, turn a wine stopper or something in 30 minutes out of free wood, it was just the perfect thing and it just took off.
- Well, I'm always amazed at what you make because it seems you always start with, what if.
How did you develop that style?
- I'm not real sure, it may have been my photography background in that in photography you can't build things.
It's there and you have to change your composition or, you know, change the time of day or whatever in order to get it.
And so you're constantly thinking about, when can I do this and how can I do that to make it better?
And wood turning was kind of the same way, when I first got into it I made the normal things that everybody else makes, but then one day you're thinking, "Well, what if I could do this?"
Or what if I could do that?
And you try to figure out a way to do it, because back when I started, we didn't have all these videos, it was, you pretty much learned on your own.
- I remember starting myself and I'd have to go to the library or try to find some old guy that would mentor me a little bit with something I wanted to learn.
Learning has changed a lot, yeah.
But there is no school for most of what you do.
(chuckles) Kind of tell us about how you develop a project.
- Well, usually there's something going on.
Early on, everybody's always saying, "You need to get out of the box."
You know, you need to think outside the box.
I find for me, it's better if I think inside the box.
In other words, if I narrow my scope on something and I say, I need to build something, such as my Louisville slugger piece, the National symposium was gonna be held next to the Louisville Slugger plant and the theme was something about baseball.
So in my mind I was constantly going back about, what can I do about baseball that's related to it?
And by narrowing it into that box, then you come up with really unique ideas.
So I was trying to make something related to baseball, and since I make hand mirrors, this is a giant hand mirror.
So I came up with this theme in Florida several years ago, there was a guy that taped a banana to the wall and he sold that for $80,000.
Somebody came later and ripped the banana off the wall, sold that for $20,000.
So I made an airbrushed appearance of a banana being ripped off the wall, put it on my baseball bat and my base.
And when I built this piece, I purposely built it without any baseballs.
So I titled the piece, "I Could Play That Game If I Had The Balls."
(Charles chuckles) The piece that we'll see up here in a little bit, it's called "The Biological Clock."
That was probably one of my first pieces that actually made a statement.
You know, I was 40 years old, my wife was 38, whatever, we were all thinking about kids and had to think about getting older and what you do.
And so I designed that piece one day and thought I could build it.
The interesting thing about that piece was having not ever had any kind of lessons in carving, it was a real challenge to carve those feet, carve those legs.
And I did so well that I won a carving competition.
They tried to get me kicked outta the competition because the people said, "No, he's a professional."
But the judges said, "No, he's a professional photographer.
He's not a professional carver."
And so I got first place.
- Well, John, show me some of your work.
- I'll be glad to.
- All right.
What a great display.
Tell us about some of your favorites.
- Well, they all have kind of a story.
This one's one of my favorites.
This is called "Love Doesn't Have Boundaries."
My cousin married a black man years ago, had two wonderful babies, there's two little miniature goblets in there, and unfortunately she died of breast cancer.
So I made this piece kind of in her honor.
And so I'm kind of proud of that.
- [Charles] Yeah, this one looks like maybe somebody carrying somebody.
- [John] Right, this was my former secretary, had heart problems, they took her to Vanderbilt, she died two or three times.
They told her she needed a heart transplant.
Unfortunately, it takes six months or longer to find a heart.
They found a heart two nights later.
But what made me make this piece was her husband came home, found her on the floor, picked her up and laid her on the couch.
I thought, how would you make that feel?
I mean, that was, so I wanted to make a piece like that.
And it kind of ties into the Bible theme of, you know, I followed you, and it ties into Marines never leaving a body behind.
So it was all kind of in my mind.
- Yeah.
That is such an emotional piece, I can tell.
Every time I've heard the story from you, you do the same thing.
- And it took me 12 years to make that.
I'd actually made the piece, it's hard to tell all the details.
I had made the feet and the heads, I wanted 'em to appear like an older person.
So I used spalted wood.
I couldn't bend these elbows.
The wood kept breaking, I tried every bending technique on the market and could never get 'em bent.
I even went to the woods and tried to find limbs that were shaped like that.
- Well, how'd you find spalted wood for?
- Well, that was the problem was none of the wood you can find is spalted.
They developed a new timber where they crushed the timber under pressure and heat and when it expands, it doesn't expand all the way and you can bend it more than normal wood.
So that allowed me to bend the pieces, but they weren't spalted.
All this spalting was done with calligraphy pens and airbrushing.
And you can see it matches exactly.
I was really proud of that.
- And so your what if kind of philosophy, what if I try this?
Can I match that spalting that nature does?
- I think that and saying, "I'm never gonna give up."
(chuckles) - [Charles] There you go.
Yeah.
- Well the Ukraine piece was, it dawned on me one day, you know, wars are held by younger men.
What happens if they all got tired of just killing each other and simply laid down their arms, irregardless of what their government said, the war would just end.
So I titled that piece, "Hope Springs Eternal."
You know, they just simply laid down their arms and said, "we're not gonna fight anymore."
- And they're linked in peace there.
- And they're tied with captured rings.
- Yeah.
Wow.
What is this one about?
- Well, this one was about the housing crisis.
When the housing crisis was going on, all the rich people were having to sell their houses or their houses were going up to be repossessed or whatever.
And so it dawned on me one day, I wonder if I can actually make the three little pigs.
And it was really a bear gluing, every one of these pieces of straw was glued individually.
These are little boxes.
They're held down with magnets, they have a lid.
And so, anyway, so I made this one.
The brick house, of course, has got a really nice yard.
It's being repossessed.
(Charles chuckles) The stick house and the straw house, of course the straw house has a little bit funkier yard and so I had to learn how to do all the diorama things, which was a lot of fun trying to learn that too.
And, and then trying to figure out how to glue all the sticks on and all the straw on was quite challenging.
- Well, John, you really like to do very delicate, how in the world did he do that, kind of work?
You've got a whole collection here of just small tables and finials and candlesticks, tell us about that.
- Well, these are dollhouse scale, the ones that I do.
I've been making those for a long time.
It's just kind of a challenge to learn how to make things like that.
And then the people on the internet, once the internet came around, they start giving you a hard time about, "Well, why didn't you put a captured ring on those goblets?"
There is one in there with a captured ring on it.
So then I started making the captured ring goblets to see how small I could go.
And the smallest ring on there is actually smaller than the zero on the date of a penny.
- Wow, I can see the captured rings.
In fact, you got two captured rings on that one.
I don't know how in the world you, I guess that is as small as you can get, right?
- No.
Well actually, I used to have three boxes.
One of 'em got lost on when I came back from a demo, on the plane when my boxes got busted open and never found all those medium sized goblets.
But the super miniature goblets are still here.
And what I used to do as a joke when I was doing demos is I would pass around the first big box and then I'd pass around the medium sized box and then I'd take the third box and pass it around and say, "These are my goblets."
And then I'd pass a box around that was totally empty and say, "Now, these are my really small goblets."
And it was a lot of fun watching people hold that box up to the light trying to see those little goblets that didn't exist.
- Oh, that's great, that's a great story.
Well, John, you're known for your hand mirrors, and this is a beautiful hand mirror, but lots of your mirrors tell a story.
Tell us about that.
- Well, hand mirrors, when I started first making the mirrors, every one was different.
They became kind of a pallet for me, in that I would take this scrap piece of wood and how do I make something unique out of this?
So they gradually kind of took off and I gradually started trying to tell stories with 'em.
- How do you tell a story with a hand mirror?
- Well, a good example might be this one, which is the Mayan calendar, we were all supposed to die in 2012.
So I came up with a design for this and it became pretty challenging because there's every kind of woodworking in here.
There's carving, there's airbrushing, there's gold leafing, there's wood burning.
turned on 13 different axises.
All of these, this is ebony, these are all carved to looked like napped flint.
I wanted it to look like a war club.
- That's amazing, what a piece of work that is.
Wow.
Well, you got some others?
- I have plenty.
- All right, show us.
- You know, I made a lot of flowered ones over the years, this just happens to be one of the latest.
Just a little carving, a little airbrushing, trying to play with it all.
I've done ginkgo leaves, I've done maple leaf flowers.
- Well, I heard about one that you did that has something to do with burning.
- Well, I made this one.
I was trying to enter a competition called Turned and Burned.
And I couldn't come up with any ideas, I was racking my brain.
And I was out burning leaves and I happened to scratch the match and went, "Oh, I can make that."
Actually, this is what happened.
I was turning epoxy one time and mixing huge amounts of thickener in the epoxy.
And apparently when you do that, it creates bubbles in the epoxy.
And so I remembered that and thought, I can make that look like a match head.
So I kind of came up with the overall theme, but how am I gonna make it fit Turned and Burned?
So I turned the opening, put the mirror in there, and then it's burned.
And it says, "Success is not the result of spontaneous combustion.
You must first set yourself on fire."
(John chuckles) Fred Shero said that, he was a hockey coach.
And so I entered in the competition, and I got a letter back from the judges.
They liked this the best of all, but they felt like it had so little turning and burning on it compared to all the other entries that they would've taken a huge amount of flak if they had made me first prize.
So what they did was they gave out the prizes to the other pieces that were actually extraordinary.
And they all personally sent me a letter saying, this is the best piece in the show, we thought, and why they, you know, did that.
So I felt pretty honored about it.
- That's wonderful.
- One of the things I've been doing over the years is trying to make some mirrors from some of the people that I respected growing up.
Of course, Alfred Hitchcock was one of the greats and I was learning airbrushing so I developed this and started learning how to burn the wood.
A lot of times I learn a technique and then I try to figure out how am I gonna use that technique on something I do.
And handwriting with a wood-burning tool is really difficult.
- So it's got "The Birds," "Rebecca," "North By Northwest," all of his movies.
- All of his movies are on here, you know, somewhere or another.
- I bet it took a good evening to do this.
- Takes patience.
(Charles chuckles) My current mirror that I'm working on, always been fascinated by Picasso and particularly his cubism style.
And so I'm building this to represent his cubism paintings.
And one of the things I'm gonna do is I'm gonna break up the glass and glue it on here so that when you look at it, you see yourself as a cubism painting.
So I got a long ways to go on this, but.
- That is pure John Lucas.
(chuckles) That is just great.
(cheerful music) (cheerful music continues) (cheerful music continues) (cheerful music continues) (cheerful music continues) Right back here we have something that is kind of new for you.
- This is a trembler, I've never made one.
I've always wanted to.
For years I always thought I had the skill, just never took the time to do it.
And so I finally made it a priority and I turned one of these, a smaller one, and I liked it but it was a little bit too small in diameter.
Each element, it needs that contrast in size to look really nice.
So I made this one the other day and it came out pretty well.
- [Charles] And is the purpose more an exercise to see if you can do it, the challenge?
- It is, in France the man that I saw do it first was Jean Francois Escoulen.
And he teaches wood turning classes over in France.
And one of the graduation projects that they have to do is a trembler because it takes a lot of skill to do it.
So you're showing everybody that I have the skill to do this as a professional turner.
- Well, you're a person you definitely don't want to challenge because you'll take the challenge, I know you well.
How do you do that, how do you keep it from just tearing all apart on the lathe?
Any little pressure?
- Well, it'll be much easier to show you because it's hard to talk about what it takes to actually do one of these.
- Okay, well let's see it.
- All right.
- John, you've laminated a piece of stock here and mounted it on the lathe.
Does this lamination help at all?
- No, it actually causes some problems.
Part of the reason I laminated was you have to have the grain running continuous from one end to the other.
So I was selecting wood outta my pile that had a continuous grain and the piece that I picked was wide enough, not thick enough.
So I built up the thickness by adding these laminating layers.
But the problem is the cherry is not as hard as the hard maple.
So it actually creates a little vibration in the tool, fights me a little bit And any vibration is transmitted to here.
- Yeah, the density of the wood changes and the strategy has to change a little bit.
- Exactly.
- Yeah, the pressure used.
But again, all the grain needed to be straight.
Any short grain, this would not make it at all.
- Right, one of the problems with turning one of these things is any mistake and the piece is history.
- (chuckles) Yeah, and you've got a unique way to support it.
- Right, this is what Jean Francois Escoulen was teaching back in the days was, what I do is I turn the pace between centers first.
then I move this away and I drill a little center hole in there to put a hanger on later.
And the tail stock is no longer supporting it.
You can kind of see that it's sticking in that hole, but all it's doing is reducing the chatter and the flex.
And as you turn every, everything starts to chatter and flex.
So you put these little string steadies in here to kind of reduce how much it can move.
And then you have to change the speed of the lathe up and down.
If I go too fast, you'll see that it starts to shimmy.
- [Charles] Yeah.
- So I can either go a little faster and see if it goes away, or I can back it back down till it stops moving.
And that's where I've gotta turn right now.
Now I can continually vary the speed.
I wanna turn as high a speed as I can, but, like you saw a minute ago, as I turned that speed up, the vibration gets too intense.
I could maybe put a third string steady right there to help that.
But we may need the third one down here, maybe a fourth one.
And right now I only have four, so.
- All right.
- But to turn, like I say, you can't make any mistakes.
So I can't get a catch.
And because the wood wants to chatter a little bit, it's like turning the lip of a bowl.
If I cut too aggressively right there, it'll run back on me and I get a catch.
So I have to be very careful at the start of the cut.
See, you can see it's kicking back.
So what I wanna do is I wanna get the tool started properly.
(tool scraping) And I need to support it with my fingers.
(tool scraping) So we'll start to cut a little more gently.
(tool scraping) Now, one of the things I've learned when I started doing these was cutting parallel to the grain is incredibly slow and causes a lot more flex.
So I found that I'll cut across the grain.
(tool scraping) And while it's still thick I can get away with cheating a little bit.
You'll notice that I'm actually scraping now instead of cutting.
(tool scraping) Take little bites, don't put any pressure on the bevel.
Then I'll reduce it some more.
Again, I can reduce it crossing the grain, I don't create as much vibration on the piece so I can kind of get by with it.
(tool scraping) So what I wanna do is get the full length of this particular element, which is gonna be roughly where my line is.
- [Charles] And all the elements were a little different.
- That's the idea is to, you wanna do different designs, different things.
You'll notice I added a captured ring here.
You wanna show your skills is part of the piece is to be able to do a different design on each one and to be able to cut very, very cleanly because you can sand, but you can only sand to a certain point.
I stopped the lathe, I was getting a little bit more chatter than I wanted.
Sometimes these wheels get just a tiny bit loose and that causes that.
And I need to go back and clean up this area.
Because when you start a cut, if the wood is out around it wants to catch the tool.
So I put the bevel on there, rotate the tool.
Again, I can't put any pressure on it.
(tool scraping) Your tool has to be sharp.
And in fact, I'm finding, which is kind of interesting to me, that I am having to sharpen more frequently on something this size than I do on a bowl because the sharpness is so critical.
If I don't have a sharp tool, any pressure I put going forward causes a problem.
(lathe whirring) (tool scraping) - [Charles] Just fascinating.
- [John] The problem is, part of the problem anyway, you're only taking off about 10 thousandths of an inch per pass.
Because much more than that and you'll break it.
- This looks like about what, an eighth of an inch here?
- It's a little bit over an eighth of an inch, 140 thousandths roughly is what those three are.
- [Charles] So you've gotta bring that one down just a little bit more.
- Yeah, you can see if you look at this one and look at that one, I've got about 50% more to go.
- There you go, this is just outstanding.
Thank you for showing us the trembler.
Thank you for showing us all of your great artwork.
It's such a pleasure.
- You too, thanks for coming by.
- I'm gonna be heading down the road to find a story of another great woodworker.
See you next time on "The Volunteer Woodworker."
(cheerful music) (cheerful music continues) - [Announcer] "Volunteer Woodworker" is funded in part by, since 1970 Whiteside Machine Company has been producing industrial grade router bits in Claremont, North Carolina.
Whiteside makes carbide bits for edge forming, grooving, and CNC applications.
Learn more at whitesiderouterbits.com.
Real Milk Paint Company makes VOC-free non-toxic milk paint available in 56 colors.
Milk paint creates a matte wood finish that can be distressed for an antique look.
Good Wood Nashville designs custom furniture and is a supplier of vintage hardwoods.
Keri Price with Keller Williams Realty has been assisting middle Tennessee home buyers and sellers since 2013.
Mayfield Hardwood Lumber, supplying Appalachian hardwoods worldwide.
Anna's Creative Lens, crafters of resin on wood decorative arts.
Visit CharlesBrockChairmaker.com for all you need to know about woodworking.
If you'd like to learn even more, free classes and a variety of subjects are available for streaming from CharlesBrockChairmaker.com.
(gentle music) (light contemporary music)
Volunteer Woodworker is presented by your local public television station.
Distributed nationally by American Public Television