Made Here
Champlain College Student Showcase
Season 21 Episode 16 | 41m 38sVideo has Closed Captions
A selection of current film work from students at Champlain College.
A selection of current work from students in the Broadcast Media Production and Filmmaking programs at Champlain College. This annual showcase offers a look at contemporary subjects and a peek inside the mind of students in Vermont, as well as their learning process.
Problems playing video? | Closed Captioning Feedback
Problems playing video? | Closed Captioning Feedback
Made Here is a local public television program presented by Vermont Public
Sponsored in part by the John M. Bissell Foundation, Inc. | Learn about the Made Here Fund
Made Here
Champlain College Student Showcase
Season 21 Episode 16 | 41m 38sVideo has Closed Captions
A selection of current work from students in the Broadcast Media Production and Filmmaking programs at Champlain College. This annual showcase offers a look at contemporary subjects and a peek inside the mind of students in Vermont, as well as their learning process.
Problems playing video? | Closed Captioning Feedback
How to Watch Made Here
Made Here is available to stream on pbs.org and the free PBS App, available on iPhone, Apple TV, Android TV, Android smartphones, Amazon Fire TV, Amazon Fire Tablet, Roku, Samsung Smart TV, and Vizio.
Providing Support for PBS.org
Learn Moreabout PBS online sponsorshipPart of These Collections
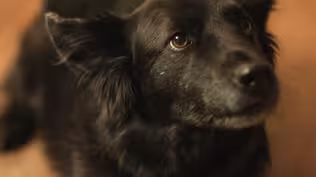
Student Filmmakers
Watch documentary and fiction films by talented young filmmakers from colleges & festivals
View CollectionProviding Support for PBS.org
Learn Moreabout PBS online sponsorshipHi I'm -Eric Ford for made here - every year on made here.
- We feature - film work from the students.
- At Champlain College.
There's always fantastic - films.
- Being made by the students, and this year is -no exception.
- Three short documentaries.
- Feature a look at sheep - farming history.
- And practice in Vermont.
- How guitars are crafted.
- Locally, - and a trip to Ireland.
- From the Champlain.
College Dublin campus.
-You can watch the 2024 -Champlain College Student.
- Showcase.
- And other great made here films -streaming on our website and through the PBS app.
- Enjoy the films.
- And thanks for watching.
- First step is talking.
- To the customer and saying, - you know what kind of guitar.
- They want it to - sound like.
- You know what I mean?
- Put the the wood choices.
- Together for sound, and then it's all about -how do you want it to look -and feel and play and sound.
- The short version.
- Of How to Make a Guitar -is cut off the wood, -get a dimension just right.
-Once the body is together, -then it goes on to the neck.
The neck gets set on here.
- It needs to be.
- At the right pitch.
-Otherwise, you know, -the strings may sit too -high or too low.
- Prep it for finish.
- Finish it.
Polish the finish, - and then it'll go to the set.
- Up room.
- Looks.
- Where it gets the strings.
- It gets the nut.
- In the saddle slot.
You know, set.
And then there's the -wiring up the electronics, -putting it all together, - playing it.
- And doing the set up.
And then - taking pictures of it.
- And sending it off to the client, -hoping they're happy.
- Oh.
Moved.
- To Burlington in 1996.
- And, I've been playing.
- Guitar quite casually for, I don't know, you know, - 6 or 7 years prior.
- To that, but.
- And also, as a day job.
- Cutting up wood and, I realized I could merge - those two.
- Things was sort of the - why didn't I think of this.
- Sooner kind of epiphany?
- It's been a.
- A long journey to get here.
- I started -as a guitar player, I guess.
- When I was in fifth grade, - my family owned.
- A manufacturer company in, - New York and then moved up.
- To Burlington in 2012.
- And that's.
- When I really started, you know, making more instruments - under the Circle Strings.
- Brand name.
Those were, - you know, custom -made one off guitars.
- For players that were, - you know, pretty expensive.
- And highly detailed, I guess about 2017, 18, - my friend Pat -was working with me.
- And he said, - why don't you try.
- And make a guitar that's, you know, a little cheaper.
- And that's when I started.
- The Irish brand.
Playing on a stage.
Somewhere, -people would take note of it -and realize - it wasn't just like an off.
- The rack guitar - and come and ask me about it.
- Afterwards.
- Those people look me up.
- And so I sort of went from - just like a basement hobby.
- To having a full time job inside of a year.
You know, Trey was, - you know, when I built the.
- First guitar for him, he was -he wasn't famous, -but he became famous.
- And, I mean, I can't.
- Put a price on that, really.
- You know?
-And he's a successful.
- Player.
People -love their instruments.
I don't know, for, for -some reason, maybe guitars, !
they're a little bit anthropomor that makes sense, that, - people have more of.
- A, like a relationship - like they might have with a.
- Pet or something like that.
I don't know.
Gentleman came -in, last year - and fell in love.
- With an Irish guitar - and ended up buying it.
- And taking it home -and then, -he came back a couple couple months later, -and was thinking more -and more about, you know, - building out his collection.
- Further, - getting something.
- Custom built for himself that was a little -higher end.
- And so we started talking.
- About, circle strings, - and then it was off.
- To the races.
His his name.
It starts with the J.
It's Jonathan, I don't know, -I won't say his last name, -but he he, - he approached us.
- And asked us to build him - a pretty special guitar.
- Out of, old growth -cedar for the top.
- And he really wanted.
- To use the back and sides - of a figured mahogany.
- From a special, - tree from Belize.
- Called the tree.
- The tree.
- The tree is, it's a enormous, -mahogany tree that -fits but was felled, -back in the 70s.
Took them years -to figure out - how to get it.
- Out of the jungle.
-And it sort of has this, -you know, mythical quality for multiple reasons.
I think one is that, -you know, it's beautiful.
- It's this beautiful.
- Figured mahogany.
- And I've seen other figured.
- Mahogany, but none that's quite -as beautiful and consistent -as as the tree is.
- There's not much of it left.
- That isn't on, milled - or turned.
- Into something already.
-So that part of this, -the rarity, the scarcity, - you know, drives.
- A lot of the prices of, - Tony Woods in particular.
- For a guitar building.
- We have an on -milled piece of it.
- That was about six figures.
- So, so it's Will Hylton.
- Is doing the neck and inlay.
- Nick Durkee is the one.
- Who did the body build.
-Esau and, Will Esther, -who'll be doing the the neck set.
-Andy Arizona will be doing.
The finish.
And storm gates.
- I'll be doing.
- A final set up on it.
So the guitar body - is comprised of basically.
- Three main parts the top, the back, - and the sides are formed.
- Through - a pretty simple process.
- Involving heat and water - to loosen up the fibers.
- Of the wood enough - to allow us to bend it.
- Over a shape, - or molds of the guitar.
- That we're working - on, then be taken out.
- And be put into a separate mold kind of boxing mold.
- Another way we can adjust.
- The the stiffness of a top - is by adding braces.
- To the inside of it.
In certain areas.
- And again, the goal.
- There is just - you add stiffness.
- To the parts we want.
But when you add braces - what you're also doing.
- Is adding weight.
So what you want to do -is then go in and carve away -weight from the braces - while still trying.
- To maintain the strength -that they're, -you know, giving the top - the back goes.
- To kind of a slow process.
- That strength to weight.
- Ratio isn't as important.
- You just want the back.
- To be just solid.
- So once those three main.
- Parts are done, - they can be -assembled together.
- In a process - called boxing up or actually.
- The assembling body.
- Together we'll add.
- This material called curving or lining around the edges - of the sides.
- For extra surface area.
- And a little bit.
- Of extra strength - to and everything.
- Will be lined up.
The top and back -will be lined up on center -with the head and and block, - and they'll be sandwiched.
- Together in a press.
- And once those once.
- That is all dried up, - they can be taken.
- Out of the press.
- It can be taken.
- Out of the mold.
- The final time -the top and back usually.
- Have a little bit of a lip, - so they'll be routed.
- Flush with the sides.
- And then once that's flush.
- The entire sides length you the edges and top and back.
Once the binding is done, -everything will be leveled - and sanded flat.
- And flush with each other.
- And then from there.
- We'll go move on to Will, - and he'll take care of the.
- The next set.
I'm the head CNC, operator - programmer engineer.
- At the shop.
Most modern guitar shops - are going to have some form.
- Of CNC capabilities.
- CNC stands for Computer.
- Numeric Control.
- It's essentially a computer.
- Guided robotic machine.
- You feed information.
- To the machine - and in turn.
- It can create parts for you.
- There's two.
- Main types of software you're going to need -for CNC.
- One is CAD software and.
- The other is Cam software.
- CAD stands for Computer.
- Aided Design and Cam stands for Computer -Aided Machining.
With those programs, - you are essentially drawing.
- Geometry, - engineering and geometry.
- And how you want it to work.
- And you can essentially.
- Create parts with the CNC from there.
What we're doing in the CNC - realm.
- Is subtractive machining.
- So you're starting.
- With a larger object - and milling it down.
- To the desired shape.
- You need.
-You see me.
- Engraving the neck -blank first, -which is laying out - all the information.
- I'm going to need.
- From there.
-It's flipped and machined.
- Precisely - to the exact angles.
- And specifications I need.
-From there it's carved, -and once it's measured, my job is complete.
The part is inspected, -measured, -and then handed off to Will.
- Esther, who is going.
- To be fitting the guitar?
- Yeah.
-So the first thing I do is.
- When I get the neck, - I kind of carve out a little.
- Hollow in the heel area.
- Then I just pull sandpaper.
- Through until - it matches the heel.
- Of the neck up with the body as tightly as possible, - and dial.
- In all of my measurements - so that the strings.
- Are going to run - straight across the neck.
- And not be too high, not be off centered.
- Glue the fretboard on.
- And then root the slots - and start carving.
- And sanding it.
After I'm done with it.
Then I go -put it on the shelf and Andy will -finish, sand out the body, -mask everything off and then start -spraying color and get some -build coats on there.
-I get the next from Will, -Esther and -just prepare them to get, -you know, color and clear, - give it a protective.
- Clear coat finish.
So that's a lot of, you know, masking off the portions that - we don't want to have color.
- Or clear coat on and then laying the stain - down into the wood directly.
- And applying the sealer and clear coat over - top of that color.
- With spray equipment - usually get about anywhere.
- From 12 to 18 coats with sanding in between.
- We let it sit.
- For a couple of weeks - after all.
- The coats have been applied, -and then it gets, -polished treatment with very high grit sandpaper.
- And and then I, hand.
- The instrument off to storm to be assembled and set up.
- Yeah.
-So first it comes in and.
- Parts, it's all taped up.
I remove the tape and make sure I don't lift - any of the lacquer.
- That Andy has so lovingly - gotten ready.
-Then you put the neck.
- And the body together.
- I check the set of the neck.
- And the bridge.
-I get it all glued up, -and then it goes -on the fingerboard, -planing and pluck, - which it scans, measures.
- All the high and low spots on the fingerboard -and gives it a perfect.
Radius, just a very important -part of the process.
Using that machine.
- And then it's time for.
- Appointments like tuners, - nut and saddle.
- Carving those by hand at that point -get strung up, -then it's going to be scanned again -under the pluck.
- So it's all scanned.
- Under tension - and the flight goes through.
- And measures the frets - this time and grinds.
- Those all down.
- So you have a perfect clean.
- Fingerboard machine.
Perfect.
Yeah.
Once it's all plucked -and we'll polish the frets, -I'll give it a quick QC, -put it in a case and, -shipped off to the customer.
It's all good to go.
- But.
This is going.
- To sound kind of weird, - but it does make me feel.
- Sort of powerful.
Not in a gross way.
-It's like wearing, you know, -a piece of beautiful jewelry or something.
- Although I don't want.
- To wear long jewelry, but.
- But I wear this guitar.
- As a piece of jewelry.
- This guitar will not rarely.
- Go out of tune.
That was a big thing for me.
- I said, like, -that's.
- Probably my number one thing - even compared to.
- Anything else.
- I just want it.
- To be really solid so it doesn't go -out of tune.
Usually, - I was really trusting.
- Creston and giving him - my thoughts.
- About what I like to play.
- I would send in.
- Sounds of guitars.
He would send me sounds -with different pickups.
What they sounded like.
- I knew I wanted something.
- A little -more intense sounding, -I guess.
- So just every detail there.
- Was, every, - you know, even.
- You know, what color, - what color.
- I wanted the pickguard to be - and what type of pickguard.
- And just every detail.
-He asked me about it.
-Of course, -I have my engraving.
- You probably heard this.
- From a lot of musicians.
- Like I'm very socially.
- Awkward generally, actually, - when I'm on stage.
- And connecting with people -in that way, -like this sort of circle - of like an unspoken.
- Sort of energy that happens.
- I feel more at home.
- Or more comfortable -in the world -than any other time, -which is really weird.
I guess.
- You know, I'd say every week.
- We get an email from -somebody new who said, -we got a guitar.
- You know, I've been looking.
- For a guitar like this - my whole life.
- That I can afford.
And most of them are - either too expensive or just.
- I haven't connected with.
-So when somebody says, -you know, I've been playing -guitar for 30, 40 years, -and I picked up your guitar - and connected immediately.
- And had to buy it, - I mean, there's nothing.
- Better, nothing better.
- When Trey Anastasio.
- From Phish got his guitar, -the day he got it, -he came here and just said - he loved it -so much and connected.
- With it immediately and, - and gave the whole shop.
- A little acoustic concert with it.
So -that was definitely the best.
Feeling Ive ever had.
- He texted me the other day.
- Saying, - this will.
- Be my lifelong guitar and, I'll never have another one.
And you know - what could be.
- Better than that?
And.
- When you think about.
- Vermont's staple industries, - you probably think of maple.
- Sirup dairy or craft beer.
-But in the mid 1800s, -Vermont's biggest product was wool.
-Looking at Vermont today, -with its - dense forests, steep slopes.
- And harsh winters.
- It's hard to imagine.
- That it could have ever been - home to open green pastures.
- Dotted with fluffy sheep.
Even more surprising - is that nestled.
- In those mountains, there's still a passionate, close -knit community of sheep - farmers, shearers.
- And spinners.
- Continuing this.
- Historic process so deeply intertwined - with the state's environment.
- And its culture.
It all starts with merino sheep.
- Centuries of selective sheep.
- Breeding - in the Iberian Peninsula.
- Led to the Merino, a breed - with soft, fine, superior.
- Quality wool and lots of it.
- The Spanish.
- Had every intention - to keep these sheep.
- For themselves.
But when Napoleon -invaded in the early 1800s, -they were forced to export.
The first place -to get them in the United States -was Vermont.
At the time, this guy - by the name of William.
- Jarvis was a U.S. Consul to Lisbon, Portugal.
- Apparently.
- He had a good eye for sheep, - so he brought some of.
- The finest merino U.S. - and rams he had and had them.
- Shipped back to his farm.
- And whether it's field.
- Or moment - in the 19th century, Vermont.
- Looked very different.
- The forests had been cut.
- For lumber, leaving vast - green pastures.
- Perfect for raising sheep.
- Vermont's.
- Settlers already had sheep, - but the wool was coarse.
- And scratchy.
The merino wool was fine.
- Texture was unlike.
- Anything they had felt, - and thus.
- Came the Vermont sheep boom.
-Between 1824 and 1840, -the population quadrupled - to 1.6 million sheep, an.
- Average of six per person.
-These sheep produced 3.7 -million pounds of wool, - which all had to be.
- Processed at mills.
- In 1836.
- There were 33 mills.
The next year -there were 334.
-And then in the 1820s, -raising sheep became - the primary agriculture.
- Enterprise in the state.
And in the 1930s, -Merino were - the state's.
- Principal livestock.
So what happened?
As it turns out, -there are better places.
Than Vermont for sheep.
Sheep need land to graze, but they can't do that -during Vermont's long, -harsh winters.
They also need shelter -and supplemental feed, -which costs money.
- Eventually, the Erie Canal.
- And the railroads connected.
- New England to the western.
- United States, - where huge swaths of land.
- Make it possible for sheep - to graze.
- Year round.
Of course, that.
Vermonters couldn't compete.
- Today, the West is still the.
- Easiest and cheapest place to raise sheep.
-Plus, -the government subsidizes - the land, -allowing farms.
- To raise flocks in the tens of thousands.
- The entire state of Vermont.
- Only has 17,000 sheep, - and they're scattered.
- On sheep farms -throughout the state, -ranging from small to tiny.
- In Berlin, Kristen Gallagher.
- And her family - raised sheep on the Dodge.
- Farm.
- We've been here on this farm.
- For 14 years, and I have worked on farms for 25 years.
There are some border, -Lester.
- Those are the ones.
- Without fuzzy faces.
- They are much more friendly.
- Than the Merinos.
Pretty.
We have chickens, -cows, sheep and two cats.
- This is one.
- Of my favorite sheep - because she's so friendly.
- And she is very curious.
At Dodge Farm, the sheep are raised for fiber.
- Once a year, -Mary Lake comes to shear.
- The flock.
Kristen -used to take her wool to mills around New England, - but the turnaround.
- Time was too long - and the wool would often.
- Get mixed with other breeds.
- So Kristen started.
- Aurora's beanery.
- It was obvious to me.
- That there is a need for this scale mill -in New England, -because a lot of people have small flocks - and specialty breeds.
- That they don't want mixed with other wool.
Thanks to all this -machinery.
- Kristen.
- And her family are able - to process wool.
- Exactly how they like.
- Much of the equipment.
- Is for cleaning the wool and improving its texture, - resulting in bags and.
- Even rooms full of fluff.
- Yesterday we had a batch.
- That was so staticky -it stuck to the ceiling, -the walls and the door.
One of the things that's - really great.
- About this equipment - is that we don't just make.
- Yarn, - we make lots.
- Of different products to - to try to offer different.
- Avenues to use that wool.
- Aurora Spinner -makes yarn in a wide.
- Variety of sizes and colors.
And then here you've got a skein of dark.
-For Kristen, -it takes about a week - to process her.
- Entire flock's wool for most of the year.
- Kristen works -with other small flock.
- Farmers from around Vermont out in the East.
-We've said, okay, well, -let's just have different.
Let's have heritage breeds.
Icelandic, Shetland.
-Lots and lots of breeds, -but different colors.
And so now you can - have yarns that look great.
- Without dyeing.
And I appeal to a wide - range of knitters.
- That appreciate the variety.
- And they appreciate things.
- Coming from a small farm.
And they can maybe be.
I like the idea of some milk?
But Vermont farmers aren't - all raising unique breeds.
- For artisan yarn.
- Processing wool is costly.
- For many farmers.
- It's more profitable.
- To raise sheep for meat, mutton, and lamb.
Chet Parsons -Farm in Richford - actually started out.
- As a cattle dairy farm.
So this is a Parsons farm.
- It's been in the Parsons.
- Family since 1919.
My grandfather wanted an experienced farmer.
Chet started teaching about - livestock.
- At the University of Vermont.
-Extension in 1985, -but the job required - knowledge.
- Of more than just cows.
- But I didn't know.
- Much about sheep, - so I went out.
- And bought a flock of 30 and then jumped right in.
- Chet only just retired.
- From sheep farming, - selling his flock.
- To Shelburne Farms in 2023.
-And for all those years, -they weren't - raised for fiber.
- They were raised for meat.
Looking at the economics, - it's not hard to understand.
- Why in Vermont, mills - buy raw merino wool.
- For around $6 a pound.
- The sheep.
- Only get shorn once a year, - and that produces.
- Only 8 to 10 pounds of wool, -so that amounts to about $60 -per sheep per year.
And that's for merino wool.
- Meat breeds have far lower.
- Quality wool, which isn't worth much.
- The wool from Chet's.
- Last shearing -season sits in his barn, -unused.
-The wool is considered, -you know, a byproduct - or something.
- That is not highly valuable.
- Some of the medium to coarse.
- Grade wool is still useful.
I mean, it's just amazing -anti-microbial products - that can be used.
- In many different ways.
- So a lot of people do.
- Want to raise fiber sheep to the challenge.
Turning wool into yarn - is a labor intensive, time.
- Consuming process.
- If farmers want to sell.
- The product themselves, - they have to pay mills.
- For their services, then figure out -how to market their product -on their own - while managing the finances.
- Of raising the sheep.
- So I figure out.
- My food costs for the winter - and my shearing costs.
- And the mill costs.
- So I know a skein costs.
- Me X amount - and then I price it.
- Accordingly.
- There's no lack of demand.
- For yarn during the Covid -19 pandemic.
- Many people took up.
- Knitting and crochet, but this new customer base isn't flocking -to local wool.
- It's easier and cheaper.
- To buy from craft store - chains, who mostly sell.
- Yarn made from plastic.
- A normal ball of acrylic.
- Yarn costs around $5, while - a skein of aurora spinners.
- Plain white wool is $30.
Plastic or rayon?
- Any any sort of synthetic.
- Processing of fiber - to make yarn has huge.
- Environmental costs.
- We pay those costs.
- And other ways to our health - to the detriment of of.
- Our waterways, of our land.
- For many years, Matt Becker.
- Has worked in environmental - cleanup for the Vermont.
- Agency of Natural Resources.
-Two years ago, when Covid 19 -had him working from home, he bought six merino sheep - from the same New York farm.
- As Kristen Gallagher.
- Life is short, and I wanted.
- To learn something new.
And being in Vermont -is an excellent opportunity -to learn anything - agricultural.
- Or farming related, because - we still have those lands.
- Available to us.
- Matt is already planning.
- To expand his flock, and what I can do is - I need to start.
- Introducing these girls - to during their last month.
- Of pregnancy.
- So they need to start.
- Getting a little bit of grain.
So we're going to give them.
Oats.
Yeah.
And.
- I'm trying to make it.
- More than a hobby.
Yes.
-Having said that, -now that I have them - and I have so few of.
- Them, they are principally.
Hi, sweetheart.
Okay.
And.
All right.
I mean.
There we go.
Well, -I was surprised to learn -that, like, -they all have personalities.
- Just like your dogs.
- Or cats do.
You got just shy one.
You got your fence jumper.
- You know, they all have.
- Their own little thing.
Vermont's small -but passionate community of fiber producers - provide a powerful support.
- Network for each other.
- But getting started is still.
- A tough road to tread.
Everybody's -really encouraging and offers advice.
But what I have realized is that we've lost - a lot of -institutional knowledge just.
- About sheep and farming.
- People like myself.
- Are learning it over again.
- Yeah, and sometimes we meet.
- People like chat - and Mary Lake.
- And Kristen, who can fill in those blanks.
- The bitter.
- Cold snow and ice serve - as a yearly reminder.
- That raising - sheep in Vermont isn't.
- And never was easy.
-But every year, -the field will thaw.
Come on, girls, come on.
- And with the arrival of.
- Spring comes new life.
Hi.
It's.
I'm Melanie and.
- Partnering.
- With local filmmakers - to bring you.
- Stories made here.
-For more, -visit Vermont public.org.
Support for PBS provided by:
Made Here is a local public television program presented by Vermont Public
Sponsored in part by the John M. Bissell Foundation, Inc. | Learn about the Made Here Fund