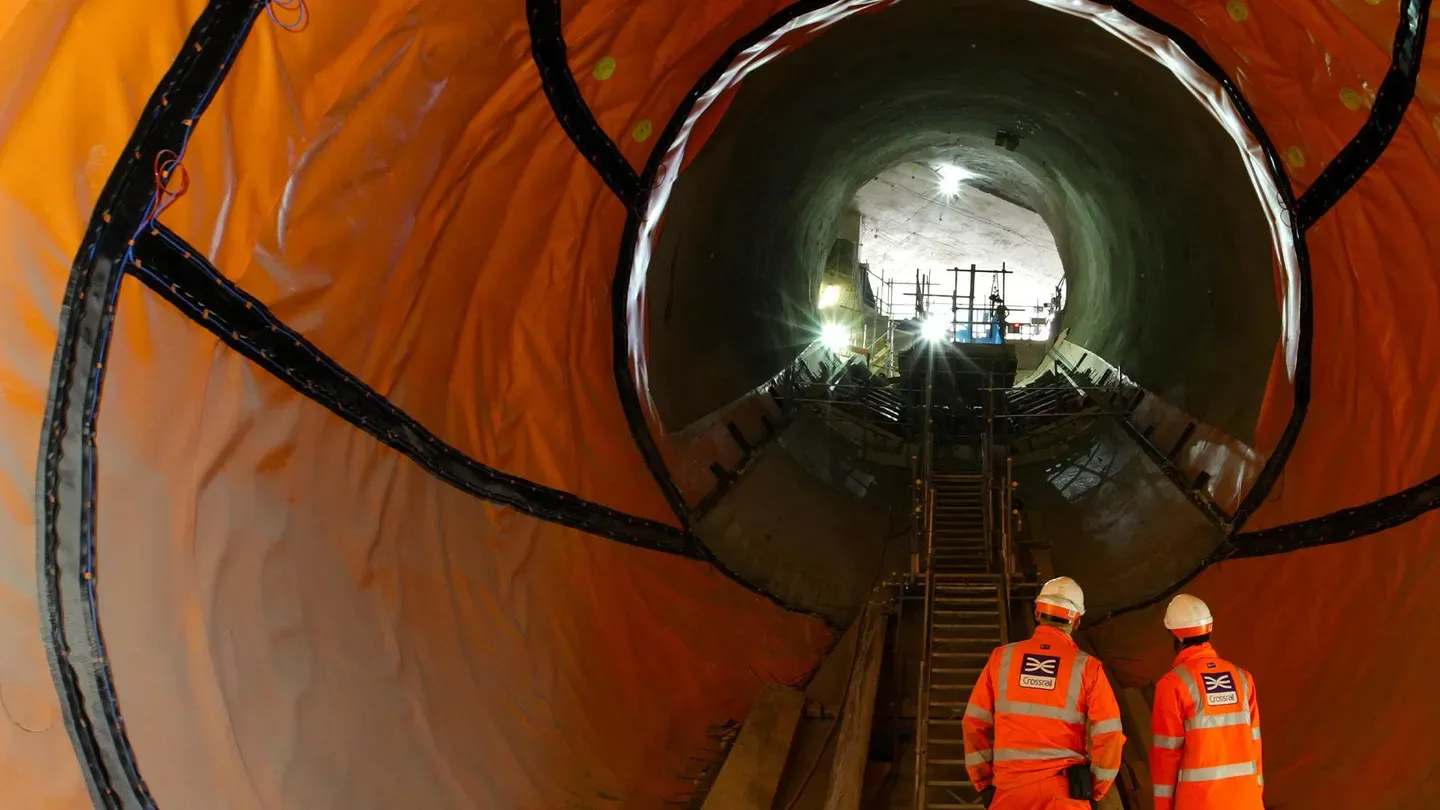
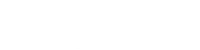
London Super Tunnel
Season 50 Episode 1 | 53m 20sVideo has Audio Description, Closed Captions
Thousands race to build Europe's biggest construction project–London's new railroad.
Thousands of engineers, technicians and workers race to build Europe’s biggest construction project–London’s new railroad, the Elizabeth Line.
See all videos with Audio DescriptionADProblems with Closed Captions? Closed Captioning Feedback
Problems with Closed Captions? Closed Captioning Feedback
Major funding for NOVA is provided by the NOVA Science Trust, the Corporation for Public Broadcasting , and PBS viewers.
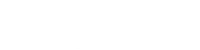
London Super Tunnel
Season 50 Episode 1 | 53m 20sVideo has Audio Description, Closed Captions
Thousands of engineers, technicians and workers race to build Europe’s biggest construction project–London’s new railroad, the Elizabeth Line.
See all videos with Audio DescriptionADProblems with Closed Captions? Closed Captioning Feedback
How to Watch NOVA
NOVA is available to stream on pbs.org and the free PBS App, available on iPhone, Apple TV, Android TV, Android smartphones, Amazon Fire TV, Amazon Fire Tablet, Roku, Samsung Smart TV, and Vizio.
Buy Now
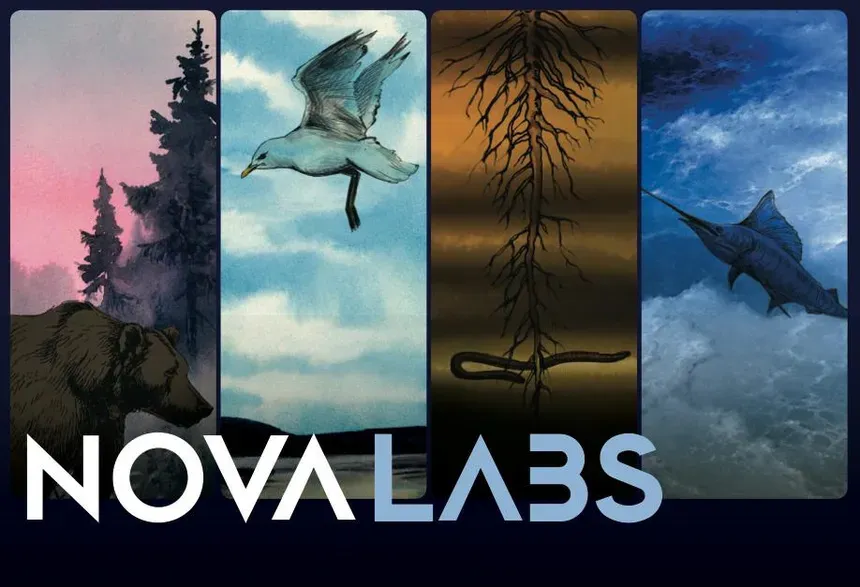
NOVA Labs
NOVA Labs is a free digital platform that engages teens and lifelong learners in games and interactives that foster authentic scientific exploration. Participants take part in real-world investigations by visualizing, analyzing, and playing with the same data that scientists use.Providing Support for PBS.org
Learn Moreabout PBS online sponsorship♪ ♪ ♪ ♪ NARRATOR: Underneath the streets of London, England, an army of more than 10,000 workers has been building a brand-new subway.
(tool whirring) Okay!
NARRATOR: It's called Crossrail.
We're under a very tight deadline.
NARRATOR: Costing nearly $20 billion, it's one of the biggest construction projects in Europe.
Give us a shout if that's gonna touch the handrail.
NARRATOR: To complete this super subway, workers must construct 26 miles of new tunnels and ten vast new stations... All right, Jez!
NARRATOR: ...laying more than 30 miles of new track...
It's the most logistically complicated programs of work I've ever, I've ever been on.
NARRATOR: ...and build 70 super-fast subway trains.
SIMON WRIGHT: It's an absolute intense battle.
NARRATOR: All under a tight deadline.
You need to get out of the way here, because trains are gonna start coming through.
NARRATOR: It's a trailblazing construction project in one of the world's busiest metropolises, and engineers face a constant battle to keep the city moving.
MAN: Constructing Crossrail is like undertaking open-heart surgery on a patient whilst that patient is awake.
NARRATOR: The oldest subway system in the world, the famed London Underground, is getting a whole new line.
More than 60 total miles of railroad in the midst of a city that never stops.
"Inside the London Super Tunnel," right now, on "NOVA."
♪ ♪ ♪ ♪ ♪ ♪ NARRATOR: London, England.
Home to more than nine million people and rising.
The key to keeping everyone moving here is the Tube.
The London Underground is the world's oldest subway system, a vast subterranean rail network handling around a billion journeys every year.
It's made up of 11 different railway lines that snake right underneath the city, allowing passengers to travel in practically any direction across the capital.
♪ ♪ But the system, which first opened in 1863, now struggles to cope with peak demand.
(station announcer speaking on P.A.)
NARRATOR: So engineers are building a brand-new underground railway line to help relieve the strain.
It will stretch across the city from the west to the east.
It's called Crossrail.
(beeping) The new railway will run from Reading and Heathrow Airport in the west through a new tunnel under Central London, connecting into existing metro stations.
It will link shopping and theater districts in the West End to the new financial district of Canary Wharf and terminate east of the city center.
It must link seamlessly into the rest of the Tube.
WRIGHT: Crossrail is a huge new railway for London, so it's going to be able to carry 200 million passengers a year, ten percent increase in capacity at a stroke.
Crossrail will help to keep London moving for the next many, many years.
NARRATOR: The projected cost of the new railway is nearly $20 billion, and work is expected to take eight years.
If the project goes according to plan, Heathrow, Europe's busiest airport, will be just 28 minutes from Central London, a journey that currently takes almost an hour on the Tube.
Preparation work on this endeavor began in 2009, launched by Boris Johnson, at the time mayor of London.
JOHNSON: This is a great day for Britain.
Three, two, one, go!
(machine creaking) NARRATOR: After three years, engineers were ready to start boring the railway's titanic tunnels.
Workers used eight giant earth-eating machines to dig the 26 miles of tunnels for the trains to pass through.
(man exclaims) NARRATOR: Excavating 3.7 million tons of earth from under London, the work was fraught with danger.
Engineers carved their way beneath fragile historic buildings, close to skyscrapers, and under the River Thames.
This part of the project took three years to complete.
But digging beneath a bustling metropolis isn't the only challenge in building this railroad.
Engineers must also begin other complex and daunting parts of the project.
They must construct ten grand stations, design and build a fleet of 70 super-fast passenger trains, lay miles of custom-designed railway track, and develop the software to control train traffic so that the first passenger services can begin.
(people cheer and applaud) NARRATOR: As the last tunnel-digging machine completes its journey...
Welcome to Farringdon!
NARRATOR: ...it's at this construction site that engineers are gearing up to build what will be one of the most impressive stations on the entire line: Farringdon Station.
Located in the heart of Central London, Farringdon is home to Smithfield Market, the largest meat market in the country, and the city's world-famous diamond quarter, Hatton Garden.
Once complete, Farringdon Station is set to become one of Britain's busiest train stations, servicing over 150,000 passengers a day.
Every day, I bounce out of bed ready to come here and come to work and feeling great about it.
NARRATOR: Project manager Linda Miller faces the mammoth task of making sure its gates open on time.
MILLER: This station is really gonna be where the action starts when the railway opens.
If you were to take the Shard, which is the tallest skyscraper in Europe right now, and lay it on its side, it would fit inside of my Farringdon Station.
We're enormous in scale.
Our platforms are over 300 meters long.
What that means in the future, if you're stepping off the trains at Farringdon, you need to know which way you're going, 'cause if you walk in the wrong direction, you're gonna be half a kilometer from where you wished you were.
♪ ♪ NARRATOR: Linda is no stranger to challenges like this.
A former U.S. Army pilot and paratrooper, Linda trained in engineering and helped build NASA's Launch Complex 40 at Cape Canaveral in Florida.
But constructing Farringdon's $918 million station will be one of her biggest tests to date.
MILLER: Looks great-- afternoon, guys.
NARRATOR: Linda's team's first task is to dig out two huge, eight-story-deep holes.
These will form the east and west concourses at Farringdon.
Underground, they must widen the freshly dug railway tunnels to create its platforms, then dig out the passageways and escalator shafts to link them to the concourses and entrances.
Excavating the earth to build the platforms is treacherous.
Minor geological fault lines run through the site and an ancient river once flowed through here, leaving the earth pitted with unstable pockets of sand and water.
The threat of groundwater running through these faults and into the tunnels is great, so they must stay vigilant as they dig through these zones.
MILLER: So this is what we've got.
Here's a bird's eye view looking down on the station.
We're facing the most dangerous type of soil.
There's not one but three different fault lines right through the middle of our work.
Fault lines present a danger.
MILLER: It provides a pathway where you could have cracks, where you could have future flooding.
NARRATOR: They use excavators to widen the train tunnels to create the platforms, carefully clawing out the earth.
MILLER: The team are digging out a mountain out from under London.
Simultaneously with the dragging away of that soil is the spraying of concrete on that face, so that the face doesn't fall in on you.
All right, Jez!
MILLER: As it flies towards the wall under pressure, it's dry, just barely, smack at the time it hits the wall.
(sprayer whirring) The mining is going well, but we're never complacent.
We never say, "Oh, yeah, we're, we, we're all that good," because that's the day it goes wrong.
NARRATOR: Once set, they line the platform walls with a plastic membrane to keep them dry.
MILLER: The membrane is fully waterproof, tough, durable, and is going to form a seal around our entire tunnel.
We are going to be wrapped like a Christmas present.
NARRATOR: With the platforms dug out and sealed here, the team at Farringdon now faces their next challenge.
To connect the stations together, builders across the line must lay more than 30 miles of brand-new rail track.
But space on site is at a premium, and installing Crossrail's track at Farringdon without disrupting other work will be no easy feat.
Gregg Purcell leads the team responsible for laying the track through this zone.
It's not often you get to work on a project of this magnitude.
It's amongst the most logistically complicated programs of work I've ever, I've ever been on in my career.
NARRATOR: Workers here will need highly specialized machinery for the task at hand.
PURCELL: This machine is called the multi-purpose gantry.
There's four of these on Crossrail, and they're worth about a million pounds each.
Looks like a Transformer, and it can change its shape depending on what condition it's working in.
NARRATOR: This mechanical marvel can lay nearly 2,000 feet of railway ties every day.
PURCELL: The multi-purpose gantries are a godsend, and I would struggle to understand how we build a project like this without that sort of kit.
NARRATOR: Once the trains start running, these tunnels will be noisy, but right here, the project faces one of its most difficult construction challenges.
The team needs to reduce the amount of noise coming from this section of track.
PURCELL: Here we are directly beneath the Barbican.
Right directly beneath.
(Beethoven's Ninth Symphony playing) NARRATOR: Opened in 1982, the Barbican Centre is an international hub for arts and culture, London's equivalent of Carnegie Hall.
The center's largest venue, Barbican Hall, sits one story below ground.
HUW HUMPHREYS: The Barbican Centre's the home of the London Symphony Orchestra, presents regular seasons from the Royal Shakespeare Company.
It really is one of the truly great artistic centers in the U.K. A lot of music is about exploring the relationship between the very quietest sounds and silence, and therefore a lot of performances really focus on that magical area of audibility.
NARRATOR: And that's the problem.
Barbican Hall sits just 55 feet above Crossrail's tunnels.
Noise or vibrations from trains could travel through the earth and into the concert hall, disturbing performances.
To guard against this, Crossrail engineers are using ingenious floating tracks, unique concrete slabs of rail track that sit on special springs.
As a train passes over these springs, they should absorb most of the energy and reduce noise reaching the theater.
PURCELL: The floating track slab allows that noise to be brought down even lower, that on the surface, you won't hear anything when you're watching "Hamlet."
NARRATOR: It takes over 150 tons of concrete reinforced with steel bars to form each 100-foot-long floating track slab.
So what you can see behind you now is all the guys assembling the track.
We've got all the reinforcements complete.
The spring housings are all installed.
We got all the rail, and this slab is being set up to cast the concrete on top.
Are we there, Steve?
Yeah, it's here now.
♪ ♪ PURCELL: There we go.
So that's the liquid gold coming out there.
♪ ♪ NARRATOR: Once set, they screw the springs into place on the underside of the slab and raise it to its final height.
With the slabs now cushioned by the springs, they can set the rails on top.
With this crucial section of the railway in place, the team can pick up the pace and lay track throughout the rest of the tunnels.
♪ ♪ Over in London's West End, the city's bustling theater district, engineers are excavating huge holes in the ground to construct another new Crossrail station: Tottenham Court Road.
And it's a challenging one, because they're doing it here, in the middle of Oxford Street, the epicenter of shopping in Britain.
With 200 million visitors every year, it's one of the busiest shopping streets in Europe, home to the famous Selfridges department store.
David Crabtree leads the team of engineers racing to build Tottenham Court Road's massive new concourse.
CRABTREE: Our station is about the size of an aircraft carrier, so if you consider constructing an aircraft carrier in the middle of London, underground, whilst keeping London going, with all its myriad of people and vehicle movements all sloshing about, that's what we've got to do at Tottenham Court Road.
NARRATOR: To build the new station here, David's team excavates two huge holes to create the concourses, a hundred feet deep and 1,300 feet apart, removing enough earth to fill 14 Olympic swimming pools.
The concourses will plug directly into the train tunnels below and the existing London Underground Tube services.
Digging vast holes like these in Central London is no simple task.
The earth around the edge of the holes is fragile and could fall in, causing the surrounding shops and buildings to collapse.
So as the team digs down level by level, they install 40 massive props to hold back the earth as they build the station's walls.
Now, with the walls complete, they face the nerve-racking task of dismantling and removing the props.
CRABTREE: So you can see here, it leaves us a nice, big open space, so we've had to put all these props in place.
However, now we need to get them out, which is gonna be an even bigger challenge.
This is engineering on a very big scale.
NARRATOR: Each 115-foot-long prop helps to hold back the weight of more than 1,500 tons of earth.
Then, as they remove the props, the newly built walls should be strong enough to resist the pressure.
CRABTREE: We're about to start removing our first big prop, and this is, this is one of the moments that we all hold our breath.
NARRATOR: With support chains attached to the first prop... GAVIN HUGHES: Come up a touch-- that's it, lovely.
NARRATOR: ...they use a mix of oxygen and propane heated to over 4,500 degrees Fahrenheit to cut out small squares in the metal.
HUGHES: They cut windows out of it, a section at a time, just to release the pressure.
NARRATOR: The more holes they cut, the weaker this prop becomes.
They hold their breath and hope that neither the prop nor walls buckle.
HUGHES: We're just at the last stage of cutting the final piece now.
You'll just see a slight bow in the steel, where all the pressure's on the smaller area, which is what it's meant to do.
It's meant to take the pressure out of it as we're cutting it.
NARRATOR: Guiding the pieces of the prop up out of the hole, through this maze of metal, will take great skill and control.
Nice and easy now, nice and easy.
MAN: Hold her there one second, hold her there.
Just up on your hoist now, up on your hoist.
(whistle blows) And up you go, all clear, up you go.
(whistle blows) Keep hoisting up.
NARRATOR: After six hours, the first prop is clear.
(whistle blows) It takes a further six months to remove all 40 props.
And with the space cleared, they work through the night to seal the building and pour the concourse's reinforced concrete roof.
MAN: Thank you, cheers.
NARRATOR: Only when the concrete has set can they begin the next stage of the work here, to finish the interiors of this colossal station.
♪ ♪ Back in Farringdon... (car horn honks) ...with platforms starting to take shape and rail tracks laid, Linda's team now faces a race to complete Farringdon Station's grand entrance hall, which has a vast and intricately designed roof.
The building must connect directly into a neighboring commuter train station.
To build its spectacular roof, Linda's team must piece together 105 custom-made reinforced concrete segments.
This will be like assembling a giant jigsaw.
42 concrete-coated steel beams will form the diamond-shaped frames.
63 concrete panels will sit inside.
Craning these awkward-shaped pieces into position without crashing into the busy train station next door will test the team's ability.
MILLER: Plugging into a live railway station has its whole set of, of new challenges.
This is the last big part of the build, and it's gonna be tough.
NARRATOR: Site manager Andy Scholes is working with Linda on this tricky build.
SCHOLES: This is our main feature of Farringdon Station.
This is what everyone will see over the next 120 year when they enter Farringdon Station.
The pressure is on in order to get this right the first time.
NARRATOR: First task: erect a network of steel supports to prop up the heavy ceiling as they lock it together.
To get all the pieces of this concrete puzzle in the right place, Andy follows his installation drawings closely.
What we have here is the plan of the ceiling itself.
Each piece is individually named and numbered, so we know where we're gonna lift them to.
If we lose the drawing, then we're, we're stuffed, basically.
Pinch up nice and easy.
NARRATOR: The beams that make up the diamond-shaped frames weigh over eight tons.
(man speaking on radio) NARRATOR: Lowering them into position, right next to the operational commuter train station, takes a delicate touch.
Keep coming down.
(whistle blowing) SCHOLES: Yep, very close.
They're moving it now to get it into position.
Yeah, down on that!
♪ ♪ SCHOLES: Touchdown.
NARRATOR: With the ceiling's frame in place, they can now slot in the diamond-shaped panels.
Pinch up nice and easy.
♪ ♪ (radio chirps) That's it, mate, all clear.
NARRATOR: Andy and the team must work fast if the station build is to remain on schedule and avoid causing a cascade of delays.
Farther east, builders are starting work on another logistically complex station build.
Whitechapel is the historic home of the foundry that cast the Big Ben bell and a market which has served locals for more than a century.
One of Crossrail's ten Central London stations will sit in this district, but the station here won't be completely new.
Instead, engineers are undertaking a $143 million overhaul of Whitechapel's existing Tube station, opened in 1876.
All right, I'm out, mate.
(laughs) NARRATOR: 76-year-old Jim Forrest manages the team tasked with building the new station here.
I've worked in construction since 1960.
I've worked on the Humber Bridge.
I worked on 1,000-foot concrete chimneys, nuclear power stations, coal power stations-- you name it.
But this is the highlight, what I'm doing now.
NARRATOR: Whitechapel is one of the most confined construction sites along the entire Crossrail line.
Market stalls, roads, and residential buildings hem the site in.
Squeezing a conventional station into such a chaotic space is impossible.
So engineers must build the new concourse on a unique 590-foot-long bridge that passes right over the site.
This station will run north to south, connecting to the Crossrail tunnels, channeling passengers to existing train lines.
A skeleton of around 6,500 pieces of steel will form its frame.
This will allow the station bridge to sit on the surrounding Victorian structures, giving the impression that it floats above the existing lines.
352 panes of glass will allow light to stream through the structure.
A steel and aluminum fire-proof roof covers the concourse, with greenery to top it off, giving this 19th-century station a 21st-century makeover.
Jim's team starts assembling the giant steel pieces that will make up Whitechapel's new floating bridge station.
FORREST: Make sure them flanges don't bite into the tarmac.
NARRATOR: They plan to use a tall crane to swing each piece into position over the existing train tracks here.
The line below is closed for today's operation, but must reopen in less than 48 hours, ready for Monday morning's rush hour.
Jim needs everything to run like clockwork if he's to avoid travel chaos.
This is a difficult operation to carry out, because the, the alignment has gotta be precise.
NARRATOR: One of the largest sections of bridge is now ready to lift.
FORREST: I can hear the tension coming into the slings and shackles now.
(metal creaking) NARRATOR: It takes great skill to carefully steer this 40-ton chunk of steel away from the buildings and down towards the railway tracks.
♪ ♪ MAN (on radio): Keep coming down.
Another little flick to your left for me.
Right, that's nice like that.
FORREST: So far, so good.
NARRATOR: This section must slot into an 82-foot-long gap.
It's going to be tight.
MAN (on radio): Go to your left a bit more, mate.
(continues speaking on radio) (metal creaking) (alarm sounding) All stop there for me a minute.
All stop there.
NARRATOR: Just as they near the drop zone, they hit a glitch.
MAN (on radio): Hit the handrail.
FORREST: What do you need to do?
Take a foot out of it?
Okay.
It's such a tight fit with the handrails, that to get the unit in, they've got to cut a small gap in the handrails.
NARRATOR: They must act fast.
A hold-up here could stop rush-hour trains running tomorrow.
Right, how's that looking on that handrail now?
MAN 2: That looks pretty sleek.
Right, we're having him come down, yeah?
MAN 3: I'm ready.
You ready, Adam, you all right?
Get ready!
MAN (on radio): Yeah, start bringing her down slowly, then.
Give us a shout if that's gonna touch that handrail.
MAN (on radio): All right, Dave, inch to go.
MAN: Right, that's us... in.
FORREST: You're looking at a very happy chappy.
Yeah, it's gone really well, that.
NARRATOR: With this giant steel section now in position, it takes around a year to install all of the 6,500 pieces.
Though the steel skeleton is a huge milestone, they still need to construct the walls, roof, and interiors if this station is going to be ready for opening.
Workers across the line are making progress.
They install wall cladding, huge ventilation fans, and miles of cabling to give the stations power.
(exclaiming) NARRATOR: Engineers have also started work on building another key element of the railway: its trains.
The railway's 70 new super-fast trains will each carry up to 1,500 passengers and come with air conditioning and Wi-Fi onboard.
We can build all the stations and track you like, but trains have to be there, as well.
NARRATOR: The $1.4 billion contract to design and build Crossrail's rolling stock has been awarded to the owners of this historic train factory in Derby, 114 miles north of London.
Workers have been building trains on this site for more than 140 years.
But constructing the Crossrail fleet will really test the mettle of these seasoned train builders.
It's a massive challenge, going from effectively a blank sheet of paper to ramping up to producing a whole fleet of trains.
It's a huge task.
MAN: And so you can see that there's a tiny gap there.
Yup.
NARRATOR: They have just 24 months to design, build, test, and deliver the first of 70 new trains-- a tall order.
Faster.
NARRATOR: Capable of traveling at speeds of 90 miles per hour, each passenger train will be over 650 feet long-- almost the length of seven basketball courts.
The team is designing their floors, walls, and roofs to be made from aluminum.
They must be compact to squeeze through the tunnels, but big enough on the inside to accommodate up to 1,500 passengers.
The trains need full air conditioning and live passenger information boards.
The stakes are high.
What time are the covers coming?
NARRATOR: It's up to 24-year-old Kane Jellyman to keep this $1.4 billion train build on track.
JELLYMAN: These are the largest-length trains we've actually produced on the site, and the largest-length trains you'll probably see on London Underground for a long while.
There's five key steps into making it look like an actual train.
The underframe comes in, which is like the floor.
The roof is loaded into the jigs.
Followed by that, we bring the body sides in.
(whirring) It's called the tubing process, 'cause this is where the shape of the vehicle actually comes together, and it looks very much like a tube.
NARRATOR: With the roof, floor, and sides of this car in place, it's time to attach the driver's cab.
Okay, it's on the way.
NARRATOR: This cab unit weighs over three tons and contains more than $325,000 worth of crucial electronics.
The electronics control everything, from the train's speed to the passenger doors and lighting.
A dent could wreck its intricate components and set the train-building schedule back.
Okay, just a box behind you there.
JELLYMAN: We don't have excess cabs in stock, so he needs to make sure he doesn't scratch it.
Do you want us to help you guide it in, Kels?
Trying to let him concentrate so he doesn't make any mistakes.
JELLYMAN: Keep coming.
Whoa.
There's a lot of money being craned there, so... God forbid if something did happen.
Couple of clicks east.
Here you go.
(crane whirring) (clangs) JELLYMAN: Nice landing.
NARRATOR: The trains must pass a series of rigorous trials before they can go into operation, from winter weather tests freezing them to -13 degrees Fahrenheit to speed and performance trials.
♪ ♪ JELLYMAN: We can't be complacent.
This is just the start.
We've got over 500 cars left to deliver, so the guys need to keep working hard and carry on delivering them.
♪ ♪ NARRATOR: Across London, stations are fitted with ticket gates, lighting, and escalators.
Here at Crossrail's new Bond Street Station, in London's luxury retail quarter, builders are installing the longest escalators on the line.
(tools whirring) Delays in tunneling and mechanical and electrical work has pushed this station build $715 million over budget and many months behind schedule.
As workers here pick up the pace, builders at Tottenham Court Road Station have completed work on its concrete roof.
LIH-LING HIGHE: You installing some signage, Mark?
(inaudible) When's it going in?
NARRATOR: Project manager Lih-Ling Highe now leads the station's interior finishing work.
This is the time when we are turning empty structures and empty tunnels into living, breathing buildings with lighting, with cladding, with fixtures, with fittings.
Being a project manager of a station on such a complex project is a bit like holding onto 400 spinning plates and making sure they're delivered in exactly the right place, whilst riding a unicycle crossing on a tightrope.
NARRATOR: Today, Lih-Ling's team is waiting for a construction train to deliver the station's platform screen doors.
HIGHE: It's really important to get the platform screen doors in, because without the platform screen doors, we're not going to be able to open the station.
NARRATOR: Engineers must install two-and-a-half miles of floor-to-ceiling platform screens in eight new stations.
The screens stop passengers falling onto the line and maintain air flow around the station.
Each screen unit is made from bombproof glass and has a straight edge.
But Tottenham Court Road's eastbound platform is a 768-foot-long curve, shaped to avoid hitting a subterranean maze of sewers, foundations, and other rail lines.
So Lih-Ling's team is relying on a construction train equipped with special robotic arms to carefully lift and connect each screen at a 0.4-degree angle from one another.
If the angle is off, the screen could jut out and collide with an oncoming train.
They must fight for every inch of space.
The more screens they install, the tighter their worksite becomes.
Lead engineer Frank Foley is in charge of installing the platform screen doors on site.
(tool whirring) FOLEY: The first step is for the train to be carefully aligned in the correct spot to start unloading the first module, to lift the module off the back of the train, and align it accurately with the brackets that are already installed on the platform.
Ready?
NARRATOR: Using a remote control, workers carefully guide the train's robotic arms to move each screen into position.
MAN: All right, coming down.
Go right a touch.
Okay, all in.
FOLEY: It's that nail-biting time when they find out if the brackets are in the right place or not.
MAN: Now go back a touch.
NARRATOR: Lining up each screen, weighing the equivalent of a pick-up truck, with its brackets takes a delicate touch.
MAN: Yeah, that's good, yeah.
It's a bit fiddly with the spanners to, uh, to do.
They do have to be careful when they're installing the doors.
MAN: Okay, all good.
FOLEY: Now, that's the first one done.
(train horn beeps) So we've still got a long way to go.
NARRATOR: Over the next nine weeks, Frank's team races to install the remaining 137 screens.
(train horn beeps) ♪ ♪ (train horn beeps) The closer they get to the end of the curved platform, the tighter the space becomes for the crew.
Excuse me, watch your back, please.
Come in, come in, come in, come in, come in, come in.
Now, hold, hold on, you have to keep, really hold the pressure.
Stop for a minute, yeah?
NARRATOR: Everyone's feeling the pressure.
MAN: Do not leave it on the wood, right, because if you break it, we're not gonna get any more for weeks.
(train horn beeps) See this metal?
Yeah.
That's what you need to put on the floor, so you need to turn it so it goes like that and then lift it up, right?
Just because I don't want the glass touching the floor.
MAN: Uh-oh.
MAN 2: Let go, let go.
MAN: All mine, all mine, all mine, all mine.
MAN: This glass needs to come up this way.
Oh-- how is it?
The tower, bring it closer.
Right, going back now, bring the tower.
It's the very last piece now.
(train horn beeps) (people talking, radio running in background) You have one bolt in.
That's it, all done.
NARRATOR: The doors are finally in, but six weeks later than originally planned.
♪ ♪ By the summer of 2018, delays completing the intricate station construction and tunnel-finishing work impact the testing of the railway, so more time and money will be needed.
Afternoon, Franz, afternoon.
NARRATOR: After seven years, work at Farringdon Station is progressing, and Linda can get her first glimpse of its grand entrance.
Wow, wow, wow, wow!
♪ ♪ That looks fantastic.
♪ ♪ It's like when you walk into a cathedral.
It is a relief, to, to finish the last of the big builds on site.
I suppose it's a little sad, too, as, as it is whenever you, you accomplish something that, that feels great.
They say diamonds are forever, but these diamonds are meant for 120 years, at least.
NARRATOR: Finishing work ramps up across the line, and by 2021, stations are slowly starting to complete, including Farringdon Station, Lih-Ling's Tottenham Court Road Station... HIGHE: This is a huge milestone.
We can see the finishing posts.
NARRATOR: ...and Jim Forrest's floating station at Whitechapel.
FORREST: This is a landmark for us, and it demonstrates to everybody here that we are capable of delivering this station as we said we would do.
NARRATOR: But the formidable scale of this engineering endeavor has pushed the project more than four years past its scheduled opening date.
The cost of the project has also spiraled to nearly $25 billion.
As work on the tunnels, platforms, stations, and trains completes, one area of the railway that is still being tested is its software.
Crossrail will be the first fully digital railway in the U.K.
It has one of the most complex systems of rail software in the world, to control everything from the trains and signals to CCTV and platform doors.
Yeah, on the screen right here... NARRATOR: The person responsible for ironing out any bugs in the software is Pradeep Vasudev.
Pradeep has nearly 40 years' experience developing computer software for transport systems, from Tube lines to military aircraft.
Crossrail has built this $13 million facility, where his team has spent more than three years testing out the software using virtual trains on virtual tracks.
VASUDEV: My interest is making sure all the bits work together.
For me, finding any issues early on is absolutely the thing we need to do.
There's nothing worse than finding it out on the railway.
NARRATOR: Their job is to push the new software to the limit, seeing how platform doors perform and discovering how the trains cope with errors.
Each version can have as many as 250 bugs that need to be rooted out and fixed.
Jim, if you can start driving the train?
♪ ♪ NARRATOR: Today, nearly 13 years after construction work first began on the project, the team is finally ready to conduct a full live trial of the railway.
This is a critical moment.
They aim to run the intended timetable service of 24 trains per hour.
VASUDEV: Today we're trying to prove that we can run a sustainable, consistent service at 24 trains per hour.
That is the ultimate timetable that we want to run for Crossrail.
We've got to a point now where we're confident that system technically can achieve it.
Everything has to work perfectly.
NARRATOR: With only two-and-a-half-minute gaps in between trains, running a fault-free service to time will be a challenge.
To do this, they will need to use a radical new feature called auto reverse.
During rush hour, trains sometimes need to switch direction to relieve the busy central stations.
To avoid the driver having to walk 650 feet to the cab at the other end, wasting valuable minutes, these trains have a much quicker solution.
When they need to do a fast turnaround to head back into the West End from Paddington Station, the driver activates an auto reverse feature that allows the train to drive itself.
In this mode, when the computer takes over, it swaps tracks and changes direction.
As it moves back into the tunnels, the driver is free to walk to the cab at the other end of the train.
Auto reverse is key to the railway hitting its 24-train-per-hour target.
The early tests of its software demonstrated that it was safe, but its real-life performance has been far from reliable.
VASUDEV: Auto reverse is absolutely crucial in our ability to run a 24-train-per-hour service.
Without it, we would struggle to run a consistent service at that level.
NARRATOR: Assisting Pradeep in the railway's control room is systems integration manager Rory Mitchell.
MITCHELL: The main thing that we've not tested before, at scale, is having trains every two-and-a-half minutes in the whole tunnel section.
So it's difficult to predict what might go wrong.
♪ ♪ NARRATOR: In West London, driver Emma Knowles will be at the controls of one of the trains.
Okay.
KNOWLES: At 24 trains per hour, this, this is a biggie today, but it's going to be fine.
It's all going to work.
(P.A.
system beeps) TRAIN ANNOUNCER: This is the TFL rail service to Paddington.
NARRATOR: Any software bugs on the trains, tracks, or station platforms during this trial could trigger serious delays across London's commuter network.
And they're off.
KNOWLES: We're off, we're moving.
NARRATOR: The team feeds more trains onto the line, all heading towards the new Underground stations.
On the platform at Paddington Station in West London, engineers must make sure that the railway's display boards are providing accurate information.
PAUL NAYLOR: So we've got a train arrived.
It wasn't due to arrive here now, so we need to check why that train turned up and isn't being shown on these screens.
Clearly, we want it to be right for our passengers when they board the trains.
♪ ♪ This train has arrived showing "not in service," whereas we would normally expect it to show "terminates here."
As you can see, we're down into the fairly small-scale issues that we're trying to deal with now.
NARRATOR: The display board faults are yet more glitches for the software team to iron out before the line can open.
Meanwhile, on the tracks...
TRAIN ANNOUNCER: This is the TFL rail service to Paddington.
NARRATOR: ...Emma pulls into Paddington.
KNOWLES: Here we go.
NARRATOR: Here, she will attempt to put the train into auto reverse: to turn it around and travel back in the opposite direction.
Is everybody off that needs to be off?
'Cause I'm closing the doors now.
Right, auto reverse.
Auto reverse.
NARRATOR: With auto reverse activated, Emma's train should now automatically move forward around a mile to change tracks, stop, switch direction, and head back east into the tunnels.
KNOWLES: So, as we come out, we're going to come out into daylight, to Westbourne Park sidings, and it's: safety, check there's no trespassers.
If there is a trespasser, emergency stop.
NARRATOR: For those used to driving trains manually, the auto mode takes some getting used to.
That's scary.
No driver!
That is so scary!
Mild heart attack.
(shudders) ♪ ♪ It's a very, very...
It's a very strange feeling that...
I'm meant to be driving it.
And we're on our way to Stratford.
The train is driving itself, modern technology.
NARRATOR: The auto reverse software on this train has worked perfectly, and allows Emma to begin her route east along the line.
Meanwhile, at Paddington, engineers are still troubleshooting problems.
DAVE: Is Stratford open now, Paul?
Yeah.
Yeah?
Yeah.
NARRATOR: They've noticed that when a train returns from completing an auto reverse maneuver, the platform screen doors aren't opening properly.
♪ ♪ (doors beeping) That didn't work, did it?
So all right, that's another one to note.
We're not sure why that didn't work, but it didn't work.
They should all open completely.
So, I think...
There you go, see?
That's the door glitch.
We need to fix it.
And we will fix it.
NARRATOR: While the team deals with door problems in West London... MITCHELL: I think we might have an issue with the trains.
NARRATOR: ...the control room is witnessing a train jam in Stratford, East London.
MITCHELL: We've now got four trains queuing up to get into Stratford, which is not going to rectify quickly.
And then we've got delays on about half of the trains.
I didn't think it would be this bad.
(watch ticking) NARRATOR: To add to their problems, another train has become stuck at Paddington.
(exhales, murmurs) MITCHELL: The train at Paddington has got quite a major failure.
The guys have been trying to reset it, so, we're, we're a bit stuck.
(chuckling): We've got 12 trains between Tottenham Court Road and Westbourne Park.
(watch ticking, people talking in background) NARRATOR: It's now up to the signalers to coordinate the trains to clear the gridlock and reboot the railway's software.
(watch ticking) MAN: Let's get it east to Farringdon and try to change ends... Yeah, yeah, yeah.
...and see if we can clear enough to... Yeah, at least we'll create some space.
Yeah, yeah, yeah, yeah.
NARRATOR: After nearly four hours of trying to reboot the software, and multiple attempts to untangle the fleet... Are you calling it, Paul?
NARRATOR: ...the team is forced to abort the test.
(people talking in background) MITCHELL: The system is brilliant at managing a steady state, and it's actually really good at managing, like, partial degradation when you've got minor delays, but when it gets to such a bad situation, and you've got a train that's blocking the line, there's not much it can do-- it can't...
It can't teleport trains around a blockage.
Because we had so many delays, we had to suspend the service and park all the trains up in the depots.
NARRATOR: The team didn't make its 24-trains-per-hour target today.
And there are still more glitches to fix.
♪ ♪ It's unfortunate, but, but it's, it's our baby, and we've got to deal with it.
NARRATOR: Over the next four months, Pradeep's team continues to test and develop the software.
♪ ♪ In May 2022, a very special visitor arrives to give the finished railway a royal seal of approval-- Her Majesty Queen Elizabeth II, in one of her final public appearances.
ANDY BYFORD: I would like to thank Her Majesty the Queen for gracing us with her presence here today.
♪ ♪ NARRATOR: The new railway is now known as the Elizabeth Line.
A week later, crowds gather to be the first to travel on the new Elizabeth Line trains.
This is a bit of history in the making, isn't it?
Exactly.
This is really a game-changer.
NARRATOR: Over two million people use the new line in the first week, helping to take the strain off London's packed Tube lines.
MARK WILD: It's been a real effort.
I'm so proud of the whole team that pulled together to make this happen.
♪ ♪ MILLER: I think in 100 years' time, people will look back at Crossrail and they will see what courage it took.
Future engineers, future British citizens will say, "This is awesome.
"This is an amazing project "that, that is for the benefit of everyone in this region."
NARRATOR: It's taken 13 years, almost $25 billion, and the determination of 75,000 workers to finally complete the largest and one of the most ambitious rail projects in the world.
♪ ♪ ♪ ♪ ANNOUNCER: This program is available with PBS Passport and on Amazon Prime Video.
♪ ♪ ♪ ♪
How Engineers Soundproof a New Underground Train Track
Video has Closed Captions
Clip: S50 Ep1 | 2m 57s | Part of the new London track is directly below an iconic performing arts center. (2m 57s)
Video has Closed Captions
Preview: S50 Ep1 | 27s | Thousands race to build Europe's biggest construction project–London's new railroad. (27s)
These Trains Take Over for Their Drivers to Cut Travel Time
Video has Closed Captions
Clip: S50 Ep1 | 2m 54s | Can trains save their drivers time by changing direction on their own? (2m 54s)
Providing Support for PBS.org
Learn Moreabout PBS online sponsorshipSupport for PBS provided by:
Major funding for NOVA is provided by the NOVA Science Trust, the Corporation for Public Broadcasting , and PBS viewers.